Picture |
Description |
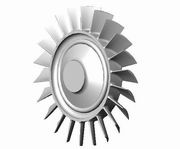 |
3D CAD model for the turbine
wheel. Turbine extracts energy from gas, and uses this energy to turn the
compressor. Yes I design my own turbine and then build it! This wheel will be
manufactured by investment casting process, out of Inconel 713LC. Since the
best nickel based heat-resistance super-alloy has been adopted, as long as
the combustion gas temperature is lower than 925 deg C, the wheel will be
very secure during operation. Diameter of this turbine : 128mm. |
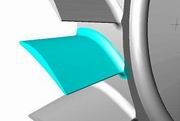 |
Closer look of 3D CAD model no.1.
A blade in high speed will suffer large resultant forces of the following :
centrifugal force, bending moment, twisting torque, etc. At the blade root
the stress is maximum, so a nice fillet
to the root of the blade is very important, this minimizes the high stress
concentration at the root, and therefore reduces the hazard of fracture greatly.
|
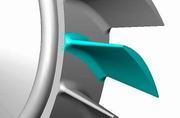 |
Closer look of 3D CAD model no.2.
Our impulse-reaction typed blade's end section
has nice gas-dynamics profile, which can operate in the supersonic range. Blade angle is determined through very
careful calculations. Thickness of the blade should be as thin as possible,
this is a must to minimize the centrifugal force under high speed, hence
helps reducing the high temperature creeping behavior of the alloy. |
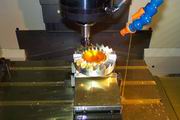 |
CNC machining the lost wax mold.
I have access to a nice 3-axis machine but it takes more than 30 hours to machine a single half !
If you take a closer look to the finished surface and you'll be amazed by
the delicacy piece of work. |
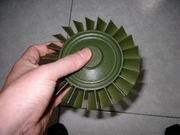 |
Wax pattern is obtained through
wax injection into the mold. You can see the video clip how I toy around with this wax
turbine at here (avi format
2.0mb), in which I used my electric fan as substitute for gas source, a
pencil as shaft, a tube as bearing, index finger as a brake (to prevent
it from going wild), all low tech but guess what ? it
works fine. |
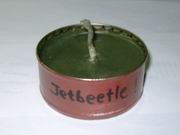 |
I have some wrecked wax patterns.
Be sure not to waste any resources, let's make it useful. Recycle it and
make some candles like this. |
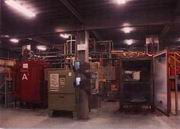 |
The foundry where my turbine is
born. From this picture
you can see equipment like vacuum hi-frequency melting furnace, and vacuum
casting chamber. As tryout purpose, we are using 304 instead of inconel. Our
304 ingot is vacuum melted, and cast in a vacuum chamber. You might dispute
that 304 doesn't need to be cast using such sophisticated equipment, but what we are doing
is to simulate accurately what will be happening when casting inconel 713LC.
|
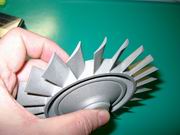 |
As-cast part out of 304 only for
casting tryout. This wheel is so critical to the project, and in fact, is
the key component for X-150, if I failed in building this item, I'll stop
the project right away with no hesitation. But take a look at this as-cast part, upon get
hold of it, I know that my project will be alive for quite a while. :-) I am very satisfied with the casting quality. |
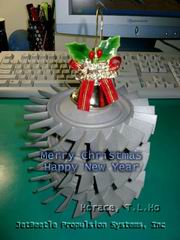 |
The world's first and only Christmas
tree made of turbine wheels ! I guarantee you won't be able to get any
of this tree
from local Christmas tree dealers because it is not for sale !
Oh Christmas tree oh Christmas
tree... |
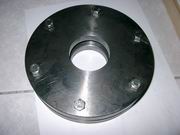 |
Boring jig. This jig will be
used very often ! The jig has open holes at both sides, so it is very
convenient to machine the turbine from the front face and rear face by
simply flipping the jig. This 2-piece jig is a unique design which
clamps the turbine wheel at the rim, and allows the operator to center the
hub. Why not center the blade root ? This wheel is a big one,
it's hub has a diameter of 30mm, quite enough for centering. My thinking is
that if the hub's circularity is bad and cannot be used to center, we should
give up centering and discard the wheel directly. |
 |
End face machining, The as-cast
part has some extra material needs to be removed. We secure the as-cast part
in the jig then have it clamped on a 3-jaw chuck. Machine away the not needed
material from both sides. At this step no centering is needed, what we
need to do is to keep the normal vector of jig face parallel to axis of
revolution, and the chuck will do this for you. In this way we can have a batch of wheels machined
very rapidly (my experience, in minutes).
Nice jig ! |
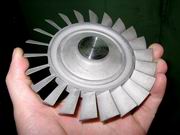 |
End face finished, we remove the jig form the chuck, open the jig and
take out the wheel for examining. Yes, it looks good! In my opinion to remove the face
material by the first cut into the hub is quite enough to get finished end
face. Now the wheel is ready for centering. |
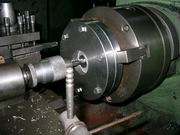 |
Boring center hole. Secure the
wheel in the jig again. Dial gauge
with probe-type stylus is needed to locate the center of the bore. Use hub to center. During
an
attempt for a once through operation the 3-flute center drill glows red hot ! Keep
the wheel in low speed and bore hole undersize. According to ISO 1940, gas
turbine is of class G2.5, under 65K RPM the eccentricity of mass center
allowed is only about 0.367μm ! Don't worry, this doesn't mean we have to
bore the hole this accurate. But after balancing the mass center deviation
should be as small as possible. |
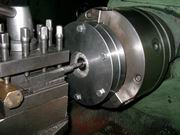 |
Reaming to size. The correct
size we need is Φ14.
when boring the undersized hole it is better to drill something like Φ10
or Φ11,
so that if the bore deviates from the center (which is quite often to occur)
we still have chance to correct it back. Both boring and reaming for SS304
we can use high-speed steel tools. However this is not the case if we are
facing Inconel 713LC! |
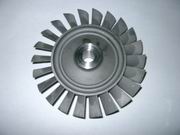 |
Completed bore hole. Please
note that this wheel is made of SS304, not the one we really want. I chose
to complete the boring work because I need a cheap part for demonstration. For the
real part we need to wait until the inconel casting is done. Since Inconel
is tough material to machine, I'll use EDM to bore the undersized hole then
ream the hole by a proper tool. |
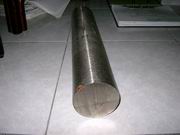 |
Inconel 713LC ingot. Bloody
expensive material. 3 tons of it worth a nice apartment in here. When into mass production there is
an important issue, that is the yield rate. We have a working
gate and runner system but we'd like to optimize it so that we can get casting parts
as many as possible. Use abrasive cutting wheel to tailor the
ingot to correct size for casting. I tried toy around using an automatic
cutting band saws with HSS saw blade to do the job. After several minutes of
wasting power, and even though those saw teeth have seen glowing red hot,
the ingot is still there unharmed. |
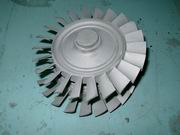 |
These are our Inconel 713LC as-cast wheels -
pretty ! Next step I'll use EDM to bore the hole undersized. |
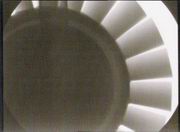 |
X Ray examination of blades. I am very
proud to announce that there's not any defects
at all. This batch of castings is a big success ! This picture is shown as
per homebuilders' request. |
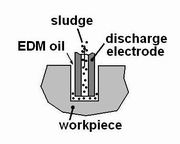 |
Finally, it's time to demonstrate how
to bore the center hole of turbine wheel by using EDM, the Electro Discharge
Machining. There is dedicated EDM drilling machine, but using ordinary EDM
can do the job as well, if we know how to handle the problem of sludge
removal. The picture shown is suction type, that is, sludge is taken away by
suction from the bottom through center hole of discharge
electrode. If your EDM can't do suction, use blow type, that is, reverse
the flow direction, this works too but leaves rough surface on the wall. |
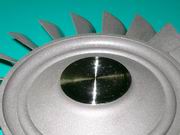 |
Preparing for EDM boring, end faces are
machined. Not much trouble encountered when machining the end face of this
Inconel 713LC wheel. However, it was not like cutting butter either, since the tool tip did not last long and several times of re-sharpening
were needed, and the machined surface is not as good as that of 304, and
some burrs at edge are very obvious, all because Inconel 713LC is especially tough.
Machining is one thing, drilling is quite another. |
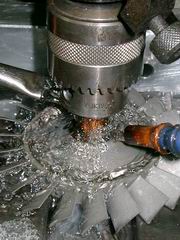 |
EDM boring in process. I use blow type,
bore hole dia. 12mm. Click on the picture to see the video clips of how
violent EDM had done to my wheel. Knife through butter ? well almost but not
quite. Disclaimer : none of my business if you hurt your neck.
:-) |
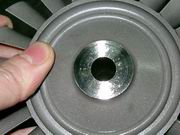 |
Completed bore hole, the hole dia is
larger than 12mm, hole wall is rough but we still have a lot of allowance
for reaming. Success ! |
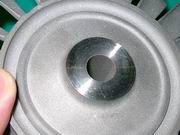 |
Yet another method of boring undersized
hole. WEDM (Wire-cut Electric Discharge Machining) it is. A copper wire of 0.2mm
diameter is
used as discharge electrode, water as working fluid, the wire cuts along
the circumference of the bore and leaves the hole. The surface is very
smooth but unfortunately it is not needed, because we will remove the
surface by reaming or grinding the hole to
size anyway. As a little conclusion WEDM is not a brutal way and is comparatively
more elegant than EDM drilling. |
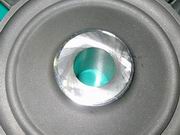 |
Finished center hole and end faces by precision
grinding. The tangential grinding pattern on end face is for increasing the friction
force. When grinding the bore, centering must be carried out at best
accuracy we can achieve, this time we cannot center the hub because there
is burr that hindered the job. So the boring jig has been improved to allow
centering the blade root. |
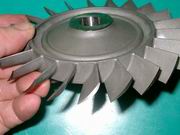 |
Turbine wheel after sizing, ready for
shipping or balancing. |
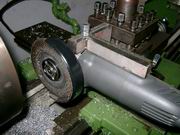 |
A low cost turbine wheel grinder,
secured to the tool post by a jig. It has not yet been validated. I call it
not-so-precise grinder, simply because the grinder vibrates alot, and is
particularly noisy. You can grind end faces, IDs, ODs, with different
abrasive wheels. |
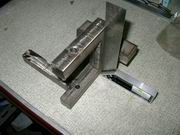 |
Grinder Jig removed from the lathe.
Laser cut from thick plate then TIG welded and drilled. Normally there
are dedicated grinding machines specially for grinding precise IDs, ODs, and
end faces. For precision purposes requirements such as low vibration and
automatic feed are necessary. |