Picture |
Description |
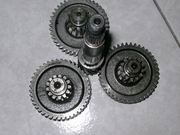 |
A good planetary gearbox is essential
for turboprop engine. After a thorough research into internet, I came
to this conclusion that no factory products for my need are available so I
must build my own. Retrofitting used gears to build the prototype
would be a great choice because they are easily available from eBay or other
popular online marketplaces. However not all parts can be
bought from internet, ring gear is the one for example. After the design is
validated all the gears will
be mass produced from blanks. Picture shows all the used parts I got for
building the gearbox. |
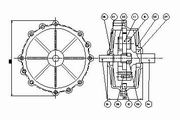 |
Planetary gearbox assembly plot. The
reduction ratio of this gearbox is : 1+99/15 = 7.6, where 15 is the number
of tooth
for sun gear, and 99 is the number of tooth
for ring gear. Use differential type if
larger reduction ratio is needed. Here's the building plan : 1. cast
aluminum housing(2 halves needed) then turn/drill/tap; 2. turn/drill/tap output
shaft; 3. turn/mill p-gear retainer; 4. retrofit p-gear by turning away the
unneeded pinion; 5. input shaft will be
used as-is, no modification needed; 6. cut ring gear; 7. source lock pins
and bolts, bearings etc. |
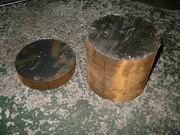 |
Rusty round stocks for turning retainer and
output shaft. You might dispute that output shaft should be turned
from casting of similar shape, rather than from such big diameter of blank. Yes, to save material and machining time,
casting is the better way for preparing it, but please remember this holds
for mass production only, for prototyping, to skip one process usually means
both more time and cost effective. So this time we chose to use directly the round stock for
convenience. |
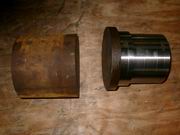 |
Shaft work in progress. Actually the
left part of this shaft is another half of the retainer, this is reason why
we need to turn such a big bar. Phew ! still a long way to go, a lot
of material need to be removed...I swear I'll cast the blank to shape,
next time. |
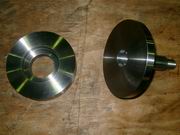 |
Lathe turning of retainer and shaft
completed. Retainer on the left, shaft on the right. |
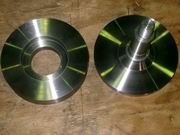 |
Lathe turning of retainer and shaft
completed. Shaft is viewed from the back. |
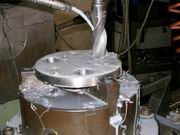 |
Reaming the bearing seat of output
shaft. The work piece is secured on an index head. Click on the picture to see the video clip. |
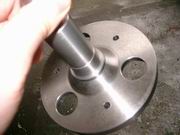 |
Drilling/milling work of output shaft
completed. Viewed from the rear. |
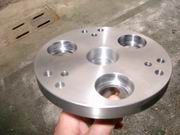 |
Drilling/milling work of output shaft
completed. Viewed from the front. From this side you see four bearing seats
and 6 lock pin holes, 3 bolt holes. |
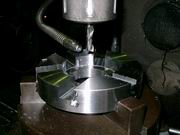 |
Milling work of retainer. Work piece is
secured on an index head, and using end mill tool to do the work. |
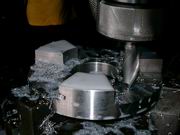 |
Retainer work piece, milling work is
still proceeding. |
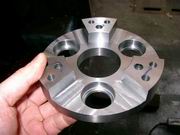 |
Retainer work piece, bearing seat
completed, holes drilled, but gear housing is still not completed. |
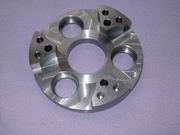 |
Retainer completed. Gear housing is
turned. In this case 4-jaw chuck is needed. |
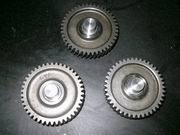 |
Engineering change No.1. After
calculation, these gears unfortunately have to be abandoned due to strength
concern. I need bigger gears for transmitting large torque. So new
gears will be cut with larger tooth width. gear housing will be changed in
accordance. |
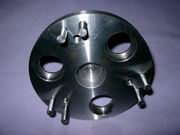 |
Shaft with lock pin inserted. These
lock pin holes were drilled with very high position accuracy, so when
assembling the other half, it won't get into trouble matching. |
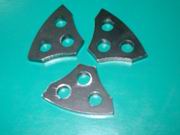 |
I need some extra space for housing
bigger planetary gears, so 3 spacers out of 6mm SS41 plate are laser cut.
Laser cut holes are accurate in position but the surface finishing is not so
good. Use drill to remove the burrs. |
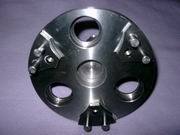 |
3 spacers are assembled onto disk of
output shaft. when pushing the spacers in place, it is really nice and easy,
fits perfectly. |
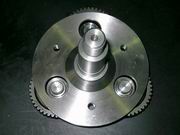 |
Well the gear + shaft assembly looks
almost like this. Bearings are still missing. |